iVT takes a visit to Volvo CE’s headquarters and proving floor in Ekilstuna, Sweden to stand up near its newly introduced mid-size electrical machines, with perception from the specialists.
With a variety of compact battery electrical machines now firmly established, Volvo Development Gear (Volvo CE) has begun the following chapter in its electrification journey, with the announcement of two midsized wheel loaders, the L90 Electrical and L120 Electrical, alongside a brand new wheeled battery electrical excavator and an electrical, cable- linked materials handler.
The primary of those autos to be made accessible to market – from the fourth quarter of 2024 – would be the 20-tonne L120 Electrical, which has a six-tonne lifting capability. The L120’s smaller stablemate, the 15-tonne L90 Electrical, stated to be the primary battery electrical wheel loader in its class, will comply with in chosen European markets in 2025.
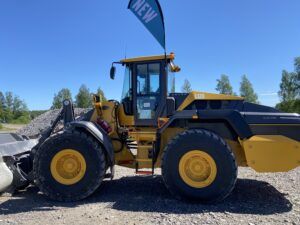
The design of the brand new electrical wheel loaders has benefited from battery expertise developed elsewhere within the Volvo Group. “It’s a Volvo electrification system,” says Fredrik Tjernström, Volvo CE electromobility options skilled. “It’s executed with the identical parts as you discover in battery electrical Volvo Vehicles.”
When it comes to battery manufacturing, Volvo CE is taking a strategic method to make sure high quality and management over their electrical machines. “There was an evolution,” says Tjerström. “Within the first compact machines we purchased batteries as full methods. However what you see within the new wheel loaders is the following degree – we purchase the modules, after which assemble the batteries in our personal factories.”
This transfer in the direction of in-house battery meeting offers Volvo better management over the standard and efficiency of their electrical machines. It additionally positions the corporate for future developments, with plans to finally produce battery cells in-house.
“Now we have began to construct our battery cell manufacturing unit in Skövde, in between Gothenburg and Stockholm [close to Volvo Group’s main powertrain plant]. So that’s the subsequent step for us,” says Tjernström.
When the battery plant was introduced in 2022 Martin Lundstedt, president and CEO of the Volvo Group stated, “Our ambition is that no less than 35% of the merchandise we promote might be electrical. This ramp-up would require giant volumes of high-performing batteries, produced utilizing fossil free vitality and it’s a logical subsequent step for us to incorporate battery manufacturing in our future industrial footprint.”
“It’s a logical subsequent step for us to incorporate battery manufacturing in our future industrial footprint”
Electrical transmission
One of the vital improvements within the new wheel loaders is the devoted electrical transmission. “We’ve eliminated the converter, which induced lots of vitality losses in a traditional wheel loader, and electrical motors are instantly linked to the transmission,” says Tjernström. This not solely dramatically improves vitality effectivity but in addition enhances machine responsiveness and the general efficiency.
The L90 and L120 Electrical characteristic separate electrical motors for hydraulics and propulsion, additional optimising vitality use and efficiency. “In a traditional wheel loader, you usually drive or function utilizing one foot on the brake and one on the gasoline pedal,” says Tjernström. “As a result of if you need full hydraulic stress to boost the bucket rapidly, you step on the brake and push the throttle to construct hydraulic stress. However within the new electrical wheel loaders there is no such thing as a relation like that. So you possibly can pull the lever hydraulic lever, and you’re going to get full hydraulic energy immediately. The accelerator pedal solely controls the drivetrain.”
This decoupled system gives operators with immediate hydraulic energy and extra exact management over the machine’s actions. Whereas the brand new management paradigm might require some adaptation for knowledgeable operators accustomed to conventional machines, it in the end leads to faster response occasions, improved vitality effectivity, and elevated productiveness via shorter cycle occasions, in addition to a extra intuitive studying curve for brand spanking new operators.
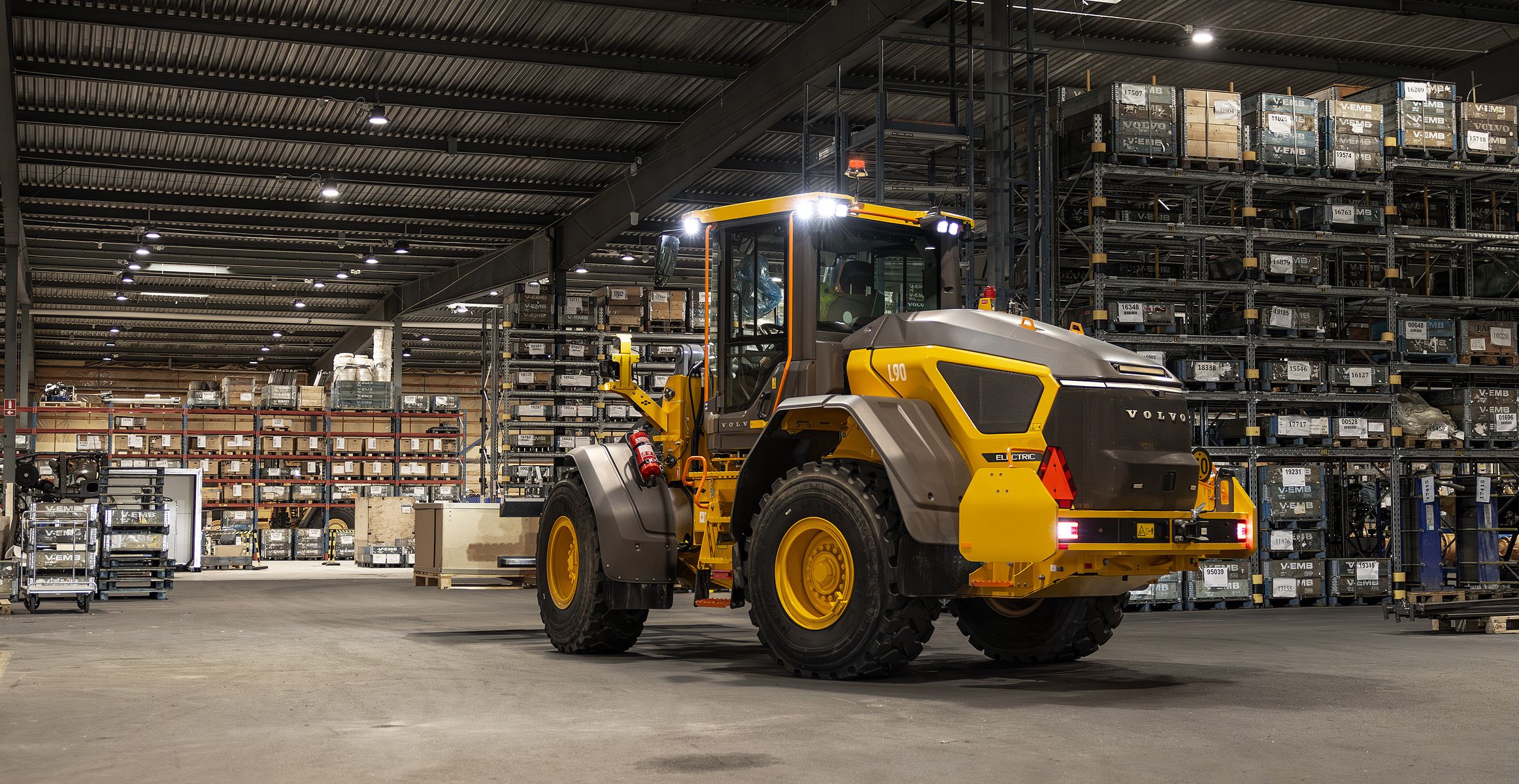
Matching diesel efficiency
A typical concern with electrical machines is whether or not they can match the efficiency of diesel counterparts. Volvo CE has addressed this head-on with the L90 and L120 Electrical. “You are able to do the identical work duties with this machine,” says Tjernström. “The distinction, after all, is the runtime.”
Nevertheless, energy autonomy ranges are nonetheless spectacular with the L120 Electrical in a position to work a full day of round 5 to 9 hours on a single cost, and the L90 Electrical lasting for roughly 4 to 5 hours of medium responsibility operation. “The secret’s to plan your working day in such a means that you just utilise non-productive time, utilizing breaks to cost the machine,” says Tjernström.
To make sure most run time Volvo CE has put appreciable thought and engineering into the battery expertise, which is temperature-controlled, that includes each cooling and heating methods to make sure optimum efficiency, whatever the local weather. “We’ve carried out in depth buyer assessments in a number of websites in China, Dubai and Australia, with very constructive suggestions,” says Tjernström.
To reinforce the convenience of vitality provision, the charging methods for the wheel loaders have been designed with flexibility and practicality in thoughts. They’re appropriate with present charging requirements, which reduces the boundaries to adoption for firms seeking to combine electrical machines into their fleets.
“You cost it with a CCS2 inlet, in order that’s the identical charging requirements you’ve gotten for vehicles or vans,” says Tjernström, “So you possibly can share the charging infrastructure on web site with different tools or autos.”
The L90 expenses from 0-100% in about 70 minutes utilizing a 150kW DC quick charger or Volvo’s PU500 cellular energy unit, whereas its AC on-board cable can energy up in six to seven hours for in a single day charging. The L120 expenses from 10-100% in a single hour 40 minutes with a 180kW DC quick charger or the PU500 and in seven hours with a 40kW DC moveable charger. Each wheel loaders even have recuperative skill, utilizing braking vitality when decelerating to cost batteries, guaranteeing an extended runtime and brake life.
Enhanced consolation and security
The advantages of the brand new electrical machines lengthen past the discount in CO2 emissions. Tjernström factors out the numerous enhancements in operator consolation and web site security: “They’ve a 3rd of the noise of the same diesel machines, but in addition a tenth of the vibrations. And that’s actually helpful for operator consolation within the work surroundings.
“Operators usually don’t consider the influence of noise and vibrations till they fight it. However then they expertise that they aren’t as exhausted afterwards as they’re after they use diesel.”
The dramatic reductions in noise and vibrations additionally make the machines extra appropriate for city environments and enclosed areas, with the discount in emissions past simply carbon lowering rapid adverse well being impacts of diesel machines. “The NOx, particulate matter and all the opposite emissions are eliminated,” says Tejernström, “In an city surroundings this reduces adverse impacts to the well being and well-being of the individuals within the metropolis, in addition to the operators.”
Electrification has additionally allowed for extra superior management methods and oftware integration. Operators can simply entry capabilities and settings from the intuitive interface, which integrates the Volvo Co-Pilot and rearview digicam when fitted.
In the meantime, the machine’s powertrain, which was beforehand managed by mechanical methods, is now managed by software program. “Earlier than it was loads in valves and hoses,” says Tejernström “However now it’s managed utilizing software program methods. This creates a brand new vary of prospects to remotely tune and customise the behaviour of the machine or the cooling system, or no matter.”
This software-centric method permits for better customisation and ongoing enhancements via updates, extending the helpful life and capabilities of the machines.
With the L90 and L120 Electrical, Volvo CE isn’t just providing new machines; they’re offering a glimpse into the way forward for development tools – a future that’s cleaner, quieter, and extra environment friendly than it has ever been earlier than.
“It’s super-exciting,” says Volvo’s new director of expertise Mats Sköldberg. “These machines will discover functions the place, from a complete value perspective, electrification can begin to make sense for purchasers. Now we’ve got the working hours, which imply the comparative value of gasoline within the diesel model will compensate their funding. We wish to exchange bigger machines which emit extra CO2 and thereby improve our influence.”
This text was first revealed within the August subject of iVT Worldwide